What is Electroless Nickel?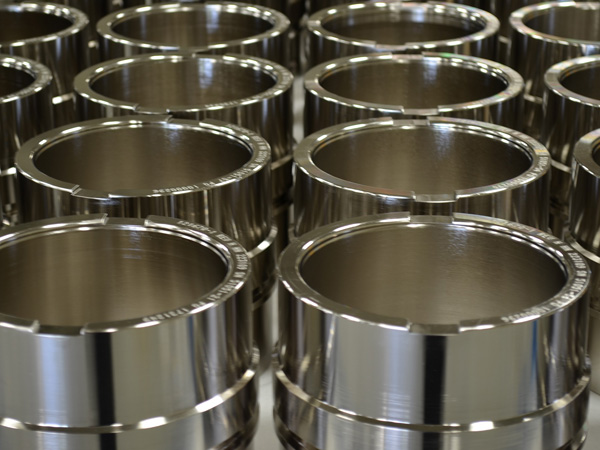
ULTRA Electroless Nickel High Phos. Alloys range from 10 to 12 percent phosphorus in nickel. When applied to substrates by autocatalytic chemical reduction, Electroless Nickel becomes a uniform, hard, and highly corrosion and wear resistant surface. Because there is no current involved in the deposition reaction, there are no current density build up concerns. The deposit is uniform all over; on corners, recesses, IDs and ODs, keeping tolerances uniform and eliminating the need for finish grinding in most cases.
Tank Sizes:
- 4′ x 4′ x 4′ tank
- 2′ x 3′ x 6′ tank
- 2′ x 2′ x 10′ tank
ULTRA Electroless Nickel Applications:
Grade Al: A premium high-phosphorus deposit which provides outstanding corrosion resistance (> 500 hrs., salt spray test). Hardness up to 65 Rockwell C after heat treatment. It provides excellent performance when used on cylinders, dies and critical parts. Meets specification requirements for MIL-C-26074, AMS 2404, ASTM B-656, ASTM B-7333, ISO 4227, GMW 3059 and Ford WSS-M99P9999A1.
Grade A2: A co-deposit of grade Al electroless nickel and PTFE (12-15% by weight). The PTFE is uniformly dispersed throughout the electroless nickel matrix to provide continual lubricity where friction is a problem.
Contact our service department for more information regarding your specific application of ULTRA Electroless Nickel.
EN Use in Multi-layer Applications
ULTRA Electroless Nickel has proven very successful in multi-layer plating applications where severe corrosion and abrasion problems exist. The Electroless Nickel/Hard Chrome/LRC combination unites to protect the substrate in the most severe environments.
Click here to download the Military Plating Specifications PDF